It is Time to Learn
New Ways to Design & Build
and Stop
doing what gets in the Way!
Examples below on
controlling machine functions, low-cost,
high-speed feeders, & ultra-low cost solar mirror drives.
In addition to his expertise showing companies how to design
machinery for manufacturability, Dr. Anderson is also an expert in designing
linkages to generate motion functions for low-cost control of repetitive
functions. To illustrate the many functions that can be generated by
linkages, he created the following model that plots out many functions from the
illustrated linkages:
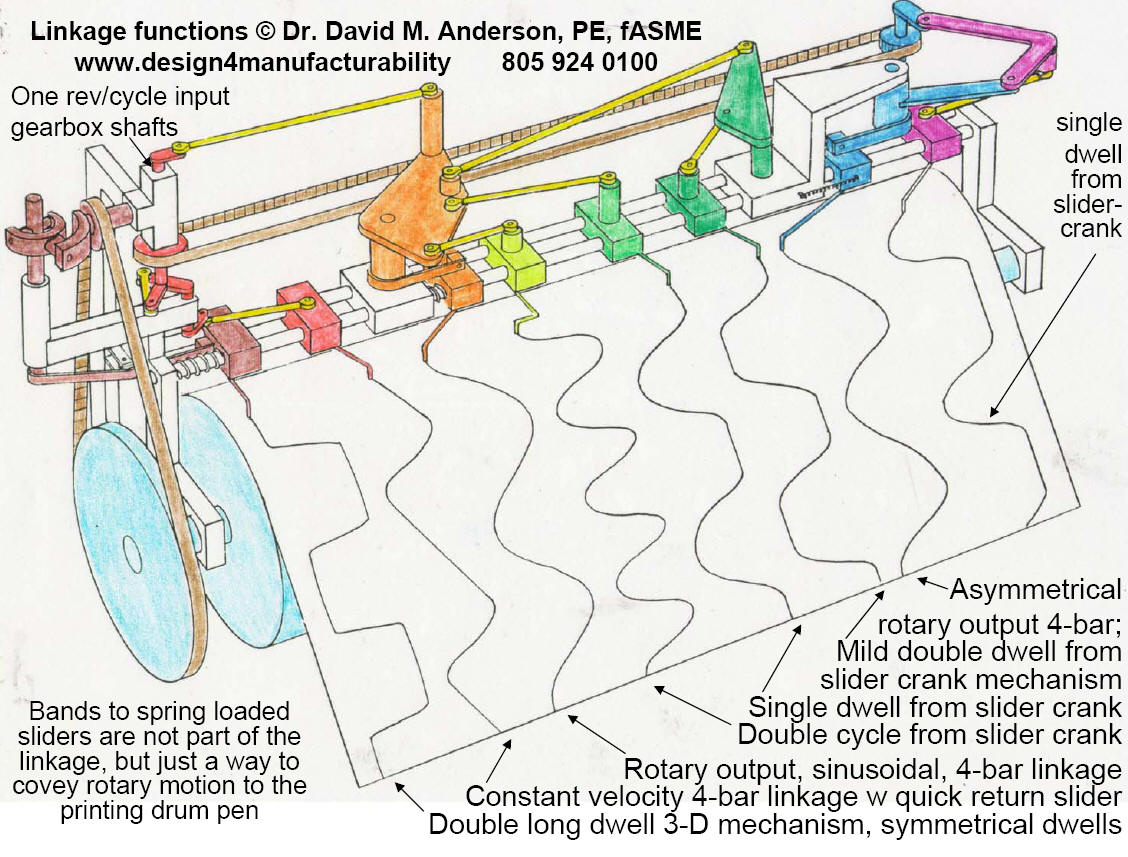
Motion Control with Linkages
Linkages provide a low-cost way to control repetitive machines. They can be
driven by any shaft rotating at one revolution per cycle. Many repetitive
machines have one of these shafts somewhere. Controlling machines with linkages
will ensure the:
Lowest Possible Cost. Linkages consist of a crank mounted on an input
shaft, driving a coupler link (usually a tube with rod end pivots on each end)
that drives an output crank. This will cost less than cams and a lot less than
computer controlled servo mechanisms or robots, either of which would be an
overly expensive overkill to .control simple repetitive motions.
Cleanest possible mechanism. Linkages are clean, open, run without
lubricants, and will not contaminate products or be affected by dirty
environments. They do not have to be enclosed to keep lubricants on cams or keep
liquids out off or electronic controllers and associated power and signal
cables.
This cleanliness makes linkage controls perfect
for food processing, pharmaceuticals, and for semiconductor fab clean rooms. In
fact, Dr. Anderson has designed ultra-clean wafer handling mechanisms that use
non-pivoting flexing bearings near semiconductor wafers. He has also designed
linkage-driven food processing to satisfy FDA cleanliness requirements.
This replaced an painted machine that was lubricated with oil and grease
with an all stainless-steel machine that was open enough to hose down and fully
inspect. It even had nozzles mounted on its pressurize frame!
Easy to build. Linkages are very easy to fabricate and assemble by
low-skilled labor. First of all, the input shaft may already be in the product
architecture as a gearmotor shaft or a gearbox shaft, or a two-shaft gearbox
would be expanded to three or four.
The input crank can be made from bar stock and be
bolted to an off-the-shelf shaft collar. The coupler link would most likely be
an internally threaded tube with off-the-shelf rod-ends or ball joints threaded
and locked to each end. The output crank may just be an arm rotating protruding
from the controlled member or the output crank would actually be the
controlled member, which would be guided and supported by the linkage (next
point).
Motion guidance. Linkages can guide and support parts or grippers
through 3-dimensional space. This would obviously be less expensive and easier
to build than separate systems for to (1) support the load on the moving
member and (2) control the motion, with more expensive cams or computer
controlled actuators.
Example # 1: Complex food processing machine controlled entirely by linkages. In order to satisfy
increasing FDA pressures for food processing cleanliness, Dr. Anderson
designed
linkage-driven machine that removed the pits from peaches, which was known as
the “Clean Pitter.” The drawing at the right, from Patent # 4,380,953, shows the
various linkages that would: orient the peach, grip it, transfer it into a pair
of blades, close the blade to grip the pit, and rotate rubber grippers in
opposite directions thus cutting the peach in half – at 90 per minute.. Since
this was a redesigns for cost, speed, and cleanliness, it preserved the “crown
jewels” of peach pitting that was refined over decades, whose motions were
guided by greased steel and controlled by a “geneva” (indexing) mechanism in an
oil bath over the food zone. This effective process is known as
commercialization that Dr. Anderson also teaches. See:
http://www.halfcostproducts.com/commercialization.htm .
The result was a low-cost, all stainless
steel machine that could easily be cleaned with its own nozzles tapped into its
pressurized frame! Since the linkage mechanisms were lighter and stronger, the
machine ran 50% faster.
To see a PDF brochure of the current version,
click on the "Clean Pitter II," link at the lower right of:
http://www.atlaspacific.com/#!peach-pitter/c6ic . (Historical
footnote: Dr. Anderson worked his way through college as a cannery mechanic
working on Atlas Pacific food processing machines.)
Example # 2: Quick-return constant-speed feeder. Dr. Anderson designed an
inexpensive 6-bar feeding linkage to drive a pusher to feed a scented pad into a
“stick up” product. In order to align the pad with the base part (which was
moving along a conveyor belt), the linkage had to push the pad at a constant
velocity, as shown in the velocity profile below. The linkage also had to return
quickly to get ready for the next stroke.
Like most machine control linkages,
the input is a one revolution/cycle input shaft, which, in this case, was in
sync with the conveyor speed. The top graphic shows a kinematic layout of
the 6-bar linkage pushing the symbol for a sliding member. The photograph
shows the scale mock-up linkage a hand crank as the input and a simulated
conveyor pockets.
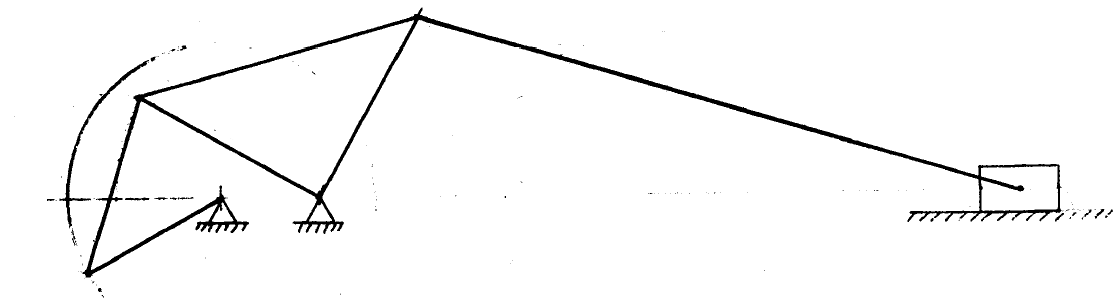
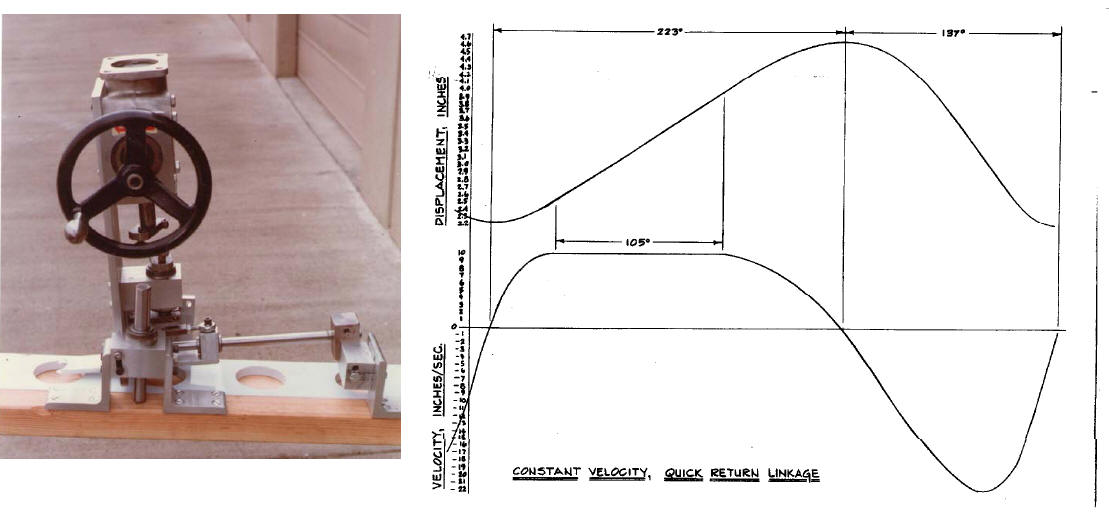
Example # 3: Linkage coupling of mirrors for ultra-low-cost
mirror guidance and 25 times better focus!. Conventional Concentrated Solar Power (CSP) power
plants use up to 350,000 “heliostat” mirrors that reflect sunlight onto a
tower-mounted target. Currently, each of these mirrors has two motors,
two gearboxes, two sets of sensors, and a computer to constantly correct both
axes all day. So a large solar field will have up to 700,000 of
these expensive control systems!
Dr. Anderson has
proven that an ultra-low-cost linkage system can couple arrays of
heliostat mirrors with low-cost linkages. This has not been done before because
no one has yet figured out how mechanically couple heliostat mirrors, since each
mirror must go through its unique daily path to reflect sunlight to a stationary
tower throughout each day. The field would thus consist of low-cost
mass-produced mirror assemblies. . The adjacent figure shows a close-up of
three coupled heliostats (with coupling linkages not shown) that individually reflect sun light at the target.
Further, focusing sunlight on the
tower can be improved 25 times!
Flat mirrors reflect un-focused light. All heliostat mirrors aim
their center at the target, but if the mirrors are flat, only the center is focused
at the target, and the rest of the sunlight shines above, below, and to the
sides of the target. This is because sunlight rays are parallel and flat mirrors
will reflect parallel sunlight rays. For instance, the outer edges
of 10 foot wide mirror will miss the target by 5 feet on each side!
Focused mirror facets can be 25 times better
focused. Sunlight focus can be improved 25 times if the heliostat consists of, say,
25 facets, each continually aimed at the target. In the above
illustration, the center mirror array shows all 25 mirror facets individually
aimed at the target, compared to the adjacent mirrors, which are
flat for a visual comparison.
Individually focused facets have been proposed
for solar furnaces (which can reach up to
3,500 oC) to replace large two-stage mirror systems (a tracking heliostat aimed at a
large fixed
parabola) with a single focusing heliostat that is focused
directly on the ultimate target. However, conventional design practice requires an extra 8 to 24
drives per heliostat. But even compromise attempts, like permanently angled
facets, won’t work on current heliostat designs that have an elevation axis
mounted over an azimuth (compass direction) axis, which rotate the mirrors
throughout the day. So, optimal
joint ordering, which is the first step in robot design, can provide (a) highly
focused mirrors and (b) stronger joint pivots.
Fortunately, Dr. Anderson can also apply
his linkage expertise to continually focus 24 “slave” mirrors on the target
throughout the day.
This brings solar furnace heat
and temperatures (UP TO 3,500 oC)
to solar power at ultra-low cost and weight.
This will be especially valuable for
generating the most heat and highest temperature for industrial processing or
heating large buildings and smaller, more compact mirror fields, where focus is
even more important. Further, larger heliostats will be possible
because (a) all mirror facets will be focused on the target (regardless of
heliostat size) and (b) structures can be stronger after getting away from an
elevation axis on top of an azimuth axis rotating on top of a pole,, which,
usually have both axes converging on a weak multi-ax-s bearing.
For Concentrated Solar Power,
(a) better focus can allow
heliostats to be closer to the tower and (b) more concentrated sunlight needs fewer
heliostats, thus resulting in more compact fields that will cost a lot less and need less land with less
permitting challenges. Further, this much greater focus can make solar
power much more feasible in northern climates and still reflect enough light to
be feasible. This, and the smaller land requirements would enable solar
replacements for fossil fuel burners in existing power plants, even in northern
climates on small or hilly sites.
These heliostats would not need field testing to verify the abovementioned
focus and functionality, since all the parts would be built on CNC machine tools
with all dimensions fabricated at +/- .001" accuracy, which is routinely
accomplished by these automated machine tools.
See how this fits into the big picture in the new white paper: "Half Cost
Concentrated Power" at:
http://www.halfcostproducts.com/half_cost_solar.html
Note that this sophistication should not to be confused with "ganged mirrors"
that bolt several mirrors onto a parabolic frame or four-bar-linkage "coupling,"
of identical frame pivots, all of which will miss the target because every
mirror in a heliostat field must be individually focused precisely as
described above.
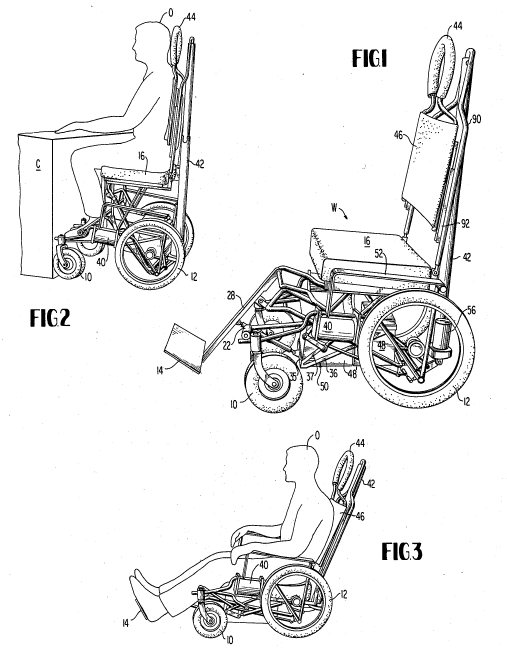
Example # 4: Elevating wheelchair. For Dr. Anderson’s thesis project,
he designed and built a wheelchair in which linkages guide and support a
quadriplegic in many positions for better comfort and to improve indoor mobility
and driving. In the illustration at the right, from patent # 3,882,949.
Figure 1 shows the powered wheelchair in the typical position.
In Figure 2, the long ball-screw actuator (behind the
back rest) elevates the seat, while pulling in the feet and narrowing the
wheelbase to be able to access high kitchen cabinets without needing leg
clearance below, which is a common problem with all other wheelchairs.
Figure 3, the seat lowers and legs extend to the
“go-cart” position for stable running on slopes and for driving in a sedan with low ceilings. Dr.
Anderson also designed and built a scale model of the concept for a
linkage-based loading mechanism which would lift the wheelchair, in the low
position, and pace it in either driver or passenger seat of a large sedan.
In the low position, the back rest can recline to redistribute body weight to
relieve and protect the skin.
The photograph below shows the first six prototypes at a
range of seat heights from the fully reclined low position to the highest
position (corresponding to Figure 2) with the foot rest pulled in to enable
reaching above kitchen counters. As the seat raised, the wheelchair width
narrowed four inches for improved indoor maneuverability.
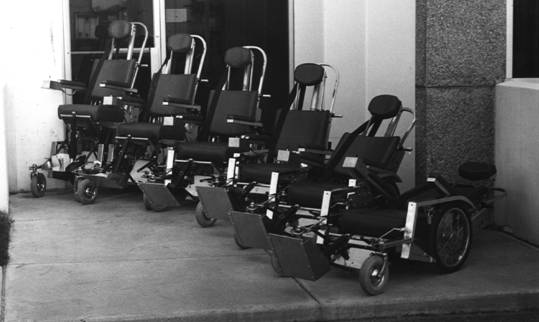
Dr. Anderson can show companies how to
incorporate these techniques into their products with
seminars and workshops or do design studies working with company engineers
to finish the implementation.
These are the general principles. Pass
around this article or URL to educate and stimulate interest
All of these
principles on DFM can be included in
your customized
class and workshop on DFM
or
the
Most Effective Product Development class
If you want to discuss Linkages & Mechanisms
by phone ot e-mail, fill out this form:
In customized seminars and
webinars, these principles are presented in the context of your
company amongst designers implementers, and managers, who can all discuss
feasibility and, at least, explore possible implementation steps
In customized workshops, brainstorming sessions
apply these methodologies to your most relevant products, operations, and supply
chains.
Call or email
about how these principles can apply to your company:
copyright ©
2021 by
David M. Anderson
Book-length web-site on Half Cost Products:
www.HalfCostProducts.com
[DFM Consulting] [DFM
Seminars] [DFM webinars]
[DFM Books] [Credentials]
[Clients] [Site Map]
[DFM article]
[Half Cost Products site] [Standardization
article] [Mass Customization article]
[BTO article] [Rationalization
article]
|